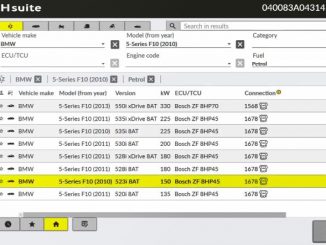
How to Diagnose and Reset DTCs on a BMW with Alientech KESS3
On June 27, 2024, Alientech introduced a new DTC (Diagnostic Trouble Code) function to their KESS3 ECU programmer. This feature allows users to view and […]
On June 27, 2024, Alientech introduced a new DTC (Diagnostic Trouble Code) function to their KESS3 ECU programmer. This feature allows users to view and […]
Attention : The KT200 ECU Programmer requires an Internet connection. 1.Click the KTsuit Manager icon to enter user registration interface 2.Input your available email and […]
This article mainly introduces CFP83 SERIES Fire Pump Drive Physical Engine Cummins INSITE 8.7 Pro 2021 Electronic Service Diagnostic Software Installation Guide Location Refer to […]
On this page we will inform You how to find out if Your Cat ET has ECM flashing possibility. 1. Hook up machine/truck/engine that You […]
Open your MB Star C4 Set you com port to Com2 , 115200 Open the EPC_Net User : admin passwd: 12345 Click “Server” Click “Edit […]
The guide is to help people who have problems in setting up BMW INPA software with VXDIAG VCX SE BMW. Setup requires USB connection Make […]
An Autel im608 user tried to clone the Citroen ECU without opening the ECU in the Immo section. Connection is easier than KTAG but IM608 […]
OTOFIX IM1 vs Autel IM508 Item Name Autel IM508 OTOFIX IM1 Remark Picture Common Immo Key Programming Yes Yes, pay for advanced license Basic Diagnostic […]
Both Ford IDS and Mazda IDS V121 software has been tested working no issue with VXDIAG scanners. Here you can download IDS v121 and patch […]
Copyright © 2025 | WordPress Theme by MH Themes